an119: Six Sigma: What? Why? How?
Application Note
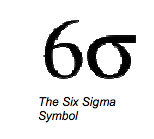
Product variation and defects undercut customer loyalty as well as company profits. Six Sigma is a rigorous, disciplined, data-driven methodology that was developed to enhance product quality and company profitability by improving manufacturing and business processes.
Six Sigma uses statistical analysis to quantitatively measure how a process is performing. That process can involve manufacturing, business practices, products, or service. To be defined as Six Sigma means that the process does not produce more than 3.4 defects per million opportunities (DPMO) – which translates to 99.9997% efficiency.
A Six Sigma defect is considered anything that can cause customer dissatisfaction, such as being outside of customer specifications. A Six Sigma opportunity is the total number of chances for a defect to occur.
Six Sigma Concept
The Six Sigma concept was developed by Motorola in 1986 with the stated goal of improving manufacturing processes and reducing product defects and variation. The underlying goal was to achieve near quality perfection with 99.9997% of variable values within specifications.Building on earlier quality improvement methods, Six Sigma assumes the following:
- Ongoing efforts to achieve stable, predictable process results are essential for business success
- Manufacturing and business processes have characteristics that can be measured, analyzed, improved, and controlled
- Sustained quality improvement requires commitment from the entire organization
Six Sigma Implementation
To achieve Six Sigma performance, the causes of manufacturing and business process defects and variation must be identified and eliminated. Two Six Sigma sub-methodologies were developed for this purpose: DMAIC (Define, Measure, Analyze, Improve, Control) and DMADV (Define, Measure, Analyze, Design, Verify).DMAIC is used to improve existing processes that are below specification; DMADV is used to develop new processes or products at Six Sigma levels. DMADV (alternatively known as DFSS [Design for Six Sigma]), can also be applied to existing processes that require more extensive improvement.
Borrowing martial arts terminology, a key innovation of Six Sigma was the creation of a professional quality management hierarchy. This structure works to involve all levels of the organization in the success of Six Sigma projects:
- Executive Leadership includes the CEO and other top management
- Champions, drawn from upper management, are responsible for Six Sigma implementation across the organization
- Master Black Belts, identified by champions or by executive leadership, function as inhouse coaches, mentors, and trainers; 100% of their time is devoted to Six Sigma to ensure business and leadership alignment
- Black Belts focus on the application of Six Sigma methodology to specific projects; 100% of their time is devoted to Six Sigma
- Green Belts are involved with Six Sigma implementation along with other job responsibilities
Lean Sigma is a current industry trend in which a process is made lean through efficiency improvements before Six Sigma is applied to reduce variation.
Six Sigma Calculation
The term “Six Sigma” comes from process capability studies, which measure the extent to which a process meets customer requirements, specifications, or product tolerances. Sigma represents the standard deviation (variation) from the process mean of a statistical population. Based on the calculation method used in process capability studies, if a process has six standard deviations between the process mean and the nearest specification limit, almost no items will fail to meet specifications. This is a Six Sigma process.The process capability index is computed using the following formula, where Cp = process capability index, USL = upper specification limit, LSL = lower specification limit, and σ = sigma:
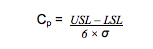
As the equation indicates, higher Cp values are found in more capable processes. As the process standard deviation goes up, or the mean of the process moves away from the center of the tolerance, fewer standard deviations will fit between the mean and the nearest specification limit, thereby decreasing the sigma number and increasing the likelihood of items outside specification.
Numerous process sigma calculators are available on the Internet that provide quick calculation of how a particular process is performing with regard to the Six Sigma goal. The calculation of a sigma level is based on the number of defects per million opportunities (DPMO). The formula to calculate DPMO is:

If, for example, there are 38 defects, 10,000 units, and one defect opportunity/unit, the results would be:
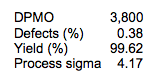
The process sigma calculation includes a 1.5 sigma shift to account for changes over time.

The 1.5 Sigma Shift
This 1.5 sigma shift was added to the calculation as a result of years of data collection by Motorola, which showed that processes vary and drift over time. Known as the Long-Term Dynamic Mean Variation, this shift is usually between 1.4 and 1.6 sigma. The reporting convention of Six Sigma, however, requires process capability to be reported in short-term sigma, which includes common cause variation but not special cause variation. As a result, short-term data typically indicates higher process capability than long-term data. To determine longterm sigma, 1.5 sigma is subtracted from the shortterm sigma calculation.Therefore, a process that fits six sigma between the process mean and the nearest specification limit in a short-term study will fit only 4.5 sigma over the long term.
In the book, Six Sigma Producibility Analysis and Process Characterization, written by Mikel J. Harry and J. Ronald Lawson and published by Motorola in 1992, there is a standard normal distribution table that is taken out to a z value of 6 (most such tables only go to a z value of about 3). Based on this table, six sigma translates to 2 defects per billion opportunities, while 3.4 defects per million opportunities – commonly defined as Six Sigma – actually corresponds to a sigma value of 4.5. A bit confusing, for sure, but the difference between short-term and long-term process performance explains it, and incorporating the shift prevents underestimating the defect levels that will probably be found over time.
Six Sigma Benefits
A definite focus on achieving measurable and quantifiable financial goals (cost reduction/profit increase) with Six Sigma projects sets this methodology apart from other quality improvement tactics. Financial benefits of potential process improvement projects are used to help prioritize the projects; these benefits are then reassessed during the analyze phase of both DMAIC and DMADV and verified in the control phase of DMAIC and the verify phase of DMADV. Closely linking Six Sigma projects to a company’s bottom line gives everyone in the organization a stake in the success of these projects. It also helps identify projects that involve critical-to-quality aspects of the process and will provide substantial process improvement.By the late 1990s, approximately two-thirds of Fortune 500 companies had started Six Sigma projects; as of 2006, Motorola had reported more than $17 billion in savings as a result of Six Sigma.
Dataforth has been involved with Six Sigma for many years and, in fact, the reliability of Dataforth’s signal conditioners is better than Six Sigma.
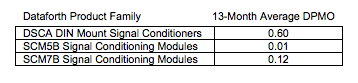
In addition to significant financial gain, Six Sigma provides organizations with the methodology and structure to make decisions based on verifiable data and statistical analysis and thereby to achieve measurable quality improvements in manufacturing and business processes. Six Sigma projects are truly a win-win situation as product quality is greatly improved while product defects and variation are reduced, employees are meaningfully involved in the outcome of the projects, company profitability is measurably increased, and customer loyalty and satisfaction are significantly enhanced.
Dataforth References
Dataforth Corp. Websitehttp://www.dataforth.com
Was this content helpful?
Thank you for your feedback!